Downtime is Costing You More Than Just Revenue – Here’s Where (and How) It’s Hitting Your Team Hardest
- Jeff Lynch
- 12 minutes ago
- 4 min read
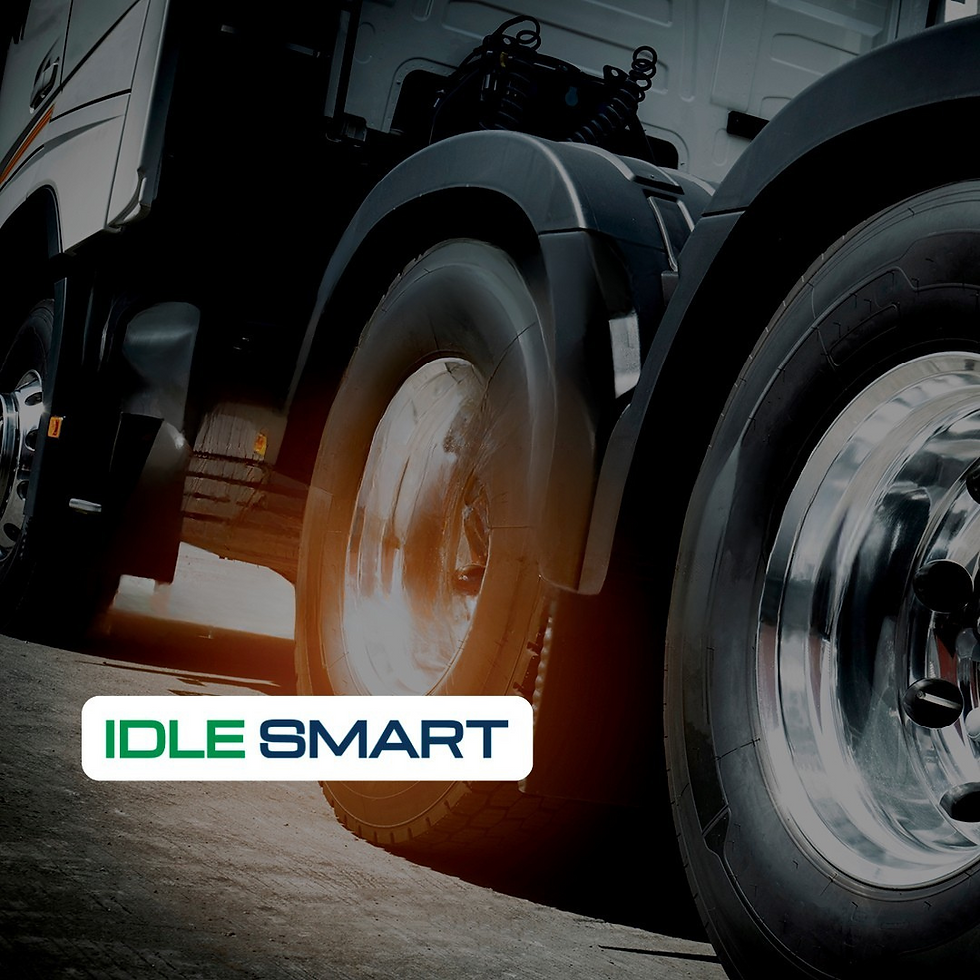
Downtime isn't just a cost; it's a relentless assault on your operation's core. It's the constant pressure of missed deliveries, the chaos of unexpected repairs, and the slow bleed of lost revenue.
For Maintenance and Operations fleet leaders, avoiding downtime isn't just about keeping trucks rolling. It means protecting your entire operation: people, partnerships, performance, and growth.
Downtime by the Numbers: Quantifying the Threat
The American Transportation Research Institute estimates downtime costs the U.S. trucking industry $448 to $760 per vehicle, per day. That's a significant hit. But the real damage multiplies when you factor in the hidden costs: lost contracts due to unreliable service, the scramble and expense of reallocating assets, the drain of increased driver turnover, and the lasting damage to customer trust. These are the costs that quickly push downtime's true impact into six-figure losses.
The real damage:
Customers bail. Repeated service failures can drive customers to switch providers.
Maintenance spirals. Unplanned events wreck shop schedules and delay planned service.
Chaos erupts. Missed routes disrupt distribution chains.
It's not if downtime costs you, but how much and how often it's preventable.
The Real Downtime Culprits: It Starts Small
Most downtime doesn't begin with catastrophic breakdowns. It starts with seemingly minor issues: voltage dips, avoidable cold starts, overlooked DPF maintenance. These small failures accumulate and interact, creating a chain reaction that disrupts operations and drives up costs.
You might track overall idle time, but are you seeing the why behind it? Are you alerted to subtle battery degradation before it leaves a driver stranded? Are you aware of comfort-driven idle overrides that are prematurely wearing down critical components?
Idle Smart illuminates these blind spots. Our system monitors critical, often overlooked indicators like battery voltage trends and excessive engine starts linked to climate control demands. By providing this granular visibility, Idle Smart allows you to proactively address issues before they escalate into costly downtime events.
The payoff:
Fewer jump starts and dead batteries, especially after overnight stops.
Reduced strain on starters, alternators, and DPFs caused by repeated idle cycling.
Lower risk of mid-route shutdowns due to overlooked voltage or thermal issues.
Downtime and the Driver Retention Crisis
In a fiercely competitive labor market, equipment reliability directly impacts driver retention. When trucks are unreliable, drivers feel the strain: missed schedules, lost rest, and constant frustration. This erodes their trust in your company and pushes them towards the exit, leading to increased recruiting costs, a less experienced workforce, and higher operational risk.
Idle Smart enhances the driver experience by ensuring consistent comfort without demanding behavioral changes. It maintains a comfortable cab environment and optimal battery levels without unnecessary idling or driver intervention, leading to fewer frustrations and a more satisfied, stable workforce.
For VPs of Ops and driver satisfaction stakeholders, this can be the difference between a one-time fix and a long-term retention strategy.
SmartPortal and SmartInsights: Turning Data into Prevention
Downtime thrives in the darkness of incomplete information. The SmartPortal provides a user-friendly interface for accessing and managing critical vehicle data. It's designed to empower users with actionable insights and granular control over their Idle Smart systems, enabling them to optimize performance, reduce costs, and maximize uptime.
SmartInsights transforms this raw data into actionable intelligence. It identifies patterns that predict downtime, often combining multiple ECM codes to provide a clear picture of potential issues. SmartInsights empowers proactive maintenance, guiding action while keeping humans in control.
For example, SmartInsights can identify:
A DPF regen issue fault
An anti-lock braking fault
A low coolant level fault
By providing early warnings of these and other potential problems, SmartInsights enables smarter service planning, minimizes unexpected failures, and provides greater control over maintenance budgets – a critical advantage for enterprise operations managing large fleets.
The Operational Cost Curve: Downtime’s Unseen Costs Multiplied
One unplanned stop doesn't just cost you that delivery. It alters the downstream flow of labor, time, and capital.
Backup vehicles need to be activated.
Drivers get reassigned or delayed.
Dispatch and maintenance scramble to realign schedules.
Customer support teams field avoidable calls.
These are hidden costs that rarely show up in budget forecasting, but they appear in profit erosion, driver fatigue, and customer churn.
Idle Smart helps smooth that curve. By reducing avoidable idle time and providing visibility into early risk indicators, the system helps maintain operational consistency at scale.
Enterprise Scalability: Built for the Complexity of Enterprise Fleets
Idle Smart was designed for enterprise operations, not off-the-shelf installation. Whether you're managing thousands of trucks across multiple regions or balancing different equipment types and operational models, Idle Smart adapts without disrupting.
The system works seamlessly across a range of truck configurations and operational environments.
Each enterprise client is paired with a dedicated Customer Success Manager to configure the SmartPortal for your fleet’s unique needs, policies, and goals.
Our training resources are designed for large-scale deployment, ensuring regional leads and key staff understand system capabilities and rollout strategy.
Once cabin comfort settings are enabled, the system operates automatically in the background without requiring daily input from drivers.
The result: faster implementation, consistent performance across the fleet, and less internal friction during adoption.
Beyond Repairs: The Brand Impact of Avoidable Downtime
Downtime affects more than delivery windows. It impacts perception.
Downtime's impact extends beyond operational costs; it affects your brand reputation. Missed commitments erode trust with enterprise shipping partners. In an era where reliability and sustainability are increasingly critical for procurement teams, a pattern of unplanned events can damage your competitive standing.
Idle Smart provides a tangible way to mitigate these risks. By delivering measurable idle reduction, proactive maintenance insights, and transparent system operation, Idle Smart supports a brand narrative of reliability and operational excellence – a crucial differentiator for executive leadership focused on long-term business value.
Downtime: From Uncontrollable to Predictable
Unplanned downtime will always pose a challenge, but it doesn't have to be a mystery. With the right data, the right alerts, and the right automation in place, most idle-related disruptions can be avoided.
Idle Smart is more than just a tool; it's a system that puts enterprise fleets back in control. By addressing the small, often overlooked factors that contribute to major downtime events, we help you improve everything from battery health to maintenance planning to driver comfort, leading to significant and lasting operational improvements.
The cost of downtime is real. But with Idle Smart, so is the return on preventing it.
Learn more about how SmartInsights and the SmartPortal can help your fleet reduce downtime, predict service needs, and protect long-term ROI.